
Selamat Datang di blog saya!
Sebelum kita menyelami kontennya, saya ingin Anda bergabung dengan saya di platform media sosial tempat saya berbagi lebih banyak wawasan, berinteraksi dengan komunitas, dan mengunggah berita terkini. Berikut cara Anda dapat terhubung dengan saya:
Facebook:https://www.facebook.com/profile.php?id=61575858997962
Sekarang, mari kita mulai perjalanan kita bersama. Saya harap Anda menemukan konten di sini yang berwawasan, menarik, dan berharga.
Daftar isi
Perkenalan
Have you ever wondered how vital air or liquids get smoothly into a fast-spinning machine? It’s thanks to the unsung heroes of motion control – pneumatic rotary joints. At Penyegelan Modern, we specialize in these critical mechanical devices that seamlessly transfer compressed air or gas from a stationary source to a rotating part, preventing kinking and downtime.
Pneumatic rotary joints, also known as swivel joints, serve a simple but important function: to ensure the uninterrupted transfer of fluids in dynamic systems. Even the slightest leak can lead to serious performance problems, machine breakdowns and high costs. That’s why industries ranging from machine tools to automotive manufacturing can’t do without these reliable, adaptable components.
In this article, we’ll look at five key benefits of pneumatic rotary joints in modern industry. You’ll learn how pneumatic rotary joints enable perfect fluid transfer, improve efficiency, extend machine life, provide superior versatility, and ultimately save you money. Let’s explore how these precision-engineered solutions can transform your industrial processes.
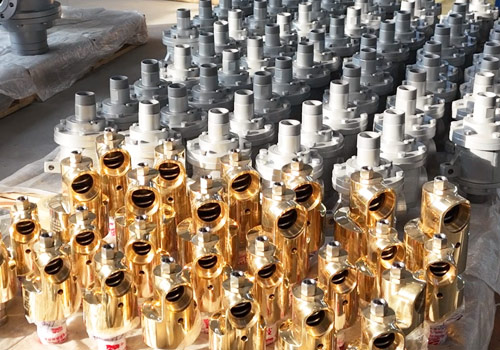
The Inner Workings: How an Air Rotary Union Delivers
To truly appreciate the benefits, it helps to understand what makes an air rotary union tick. This device creates a secure, sealed connection between your fixed air supply and the rotating part of your machine. As your machine’s component spins, the air rotary union’s internal mechanism engages, allowing compressed air to flow smoothly into your equipment. The air stays contained within the union during rotation, then releases precisely when internal valve openings align with the outlet. This clever design ensures a continuous flow without any twisting or damage to your supply line. It’s this meticulous engineering and advanced sealing that allows air rotary unions to maintain consistent performance, prevent leaks, and avoid pressure loss, even during continuous 360-degree rotation under high pressure and constant movement.
This reliability isn’t by chance. It’s the direct result of an unwavering commitment to precision in manufacturing. When you hear about “precision engineering,” “advanced sealing mechanisms,” “precise tolerances,” or “micron-level flatness control” for sealing faces, you’re hearing about the foundation of a high-quality air rotary union. This attention to detail ensures exceptional leak-free transfer, superior efficiency, and an extended operational life for your machinery.
Every air rotary union is typically built from four core components that work together seamlessly:
- Housing (Stator): This is the stationary outer shell that holds everything together and connects to your fluid supply line. Often made from durable materials like stainless steel or aluminum, its choice depends on factors like corrosion resistance and structural stability.
- Shaft (Rotor): This is the rotating part that carries the air or fluid through the air rotary union to your machine. It spins independently of the housing.
- Bearings: These are vital for supporting the rotating shaft and minimizing friction, ensuring smooth, effortless rotation. You’ll find various types, with some even “lubricated-for-life” to reduce your maintenance needs.
- Seals: Arguably the most critical components, seals are designed to prevent or minimize leakage between the rotating and stationary parts, all while keeping friction and wear to a minimum. They come in many forms, from simple O-rings to advanced mechanical seals, often using specialized materials like carbon graphite, silicon carbide, or PTFE.
The materials used in an air rotary union are chosen with extreme care. Stainless steel, aluminum, brass, carbon graphite, silicon carbide, and PTFE are common choices, each selected for properties like corrosion resistance, wear resistance, and suitability for specific temperatures, pressures, and speeds. For example, silicon carbide is highly valued for its exceptional performance under “high load, high speed, and extreme conditions,” offering superior resistance to abrasion, chemical corrosion, and thermal shock. This shows you that material choice isn’t random; it’s a critical engineering decision that directly impacts the durability, reliability, and suitability of an air rotary union for your specific application.
Air rotary unions can also be classified by their channel configuration:
- Single Passage Unions: Designed for transferring just one fluid or gas.
- Multi-Passage Unions: These allow you to transfer multiple media (like air, coolant, and lubricant) simultaneously through independent paths, preventing any mixing or cross-contamination. Some can even have up to 24 channels!
- Dual-Passage Unions: A common multi-passage type, often used in specific pneumatic applications like clutches and brakes.
Beyond this, air rotary unions are also distinguished by their speed capabilities (low-speed vs. high-speed) and the specific sealing technologies they employ, all tailored to meet diverse industrial demands.
The Five Game-Changing Advantages of Air Rotary Unions
Air rotary unions are more than just components; they are essential enablers of modern industrial excellence. Let’s explore the five transformative benefits they bring to your operations.
1: Ensuring Seamless, Leak-Free Fluid Transfer
The most fundamental role of an air rotary union is to create a perfect seal between stationary and rotating parts, preventing any compressed air or gas from escaping. This sealing integrity is absolutely critical for maintaining the smooth operation of your machinery. Advanced sealing technologies, like spring-loaded mechanical seals and specialized materials such as carbon graphite or PTFE, are meticulously engineered to minimize friction and wear while ensuring a robust seal. Innovations like Pop-Off® and AutoSense® even prevent premature seal damage from dry running by separating seal faces when pressure is off or adjusting to media conditions.
The benefits of effective sealing go far beyond just avoiding drips. They impact the entire integrity of your operation, directly influencing safety, environmental protection, and product quality:
- Operational Safety: Leaking compressed air can create serious safety hazards in your workplace. A reliable air rotary union significantly reduces these risks, ensuring a safer environment for your team.
- Environmental Protection: Preventing leaks means you’re not wasting compressed air, which translates into energy and resource conservation. This minimizes your environmental footprint.
- Product Quality: In applications where air purity or consistent pressure is paramount, leak-free operation prevents contamination and maintains precise process control, directly impacting the quality of your final product. Multi-passage air rotary unions, with their independent channels, are especially vital for preventing cross-contamination between different media.
This focus on system integrity is about protecting your entire operation from critical failures and quality compromises. Choosing a high-quality air rotary union isn’t just about avoiding minor issues; it’s about safeguarding your personnel, the environment, and the integrity of your products. This highlights the strategic importance of investing in superior sealing technology.
2: Enhanced Operational Efficiency and Productivity
An air rotary union dramatically optimizes your machine’s performance by ensuring a continuous flow of air, thereby minimizing operational interruptions.
- Uninterrupted Operation: An air rotary union ensures that compressed air or gas flows smoothly and consistently to your rotating machinery. This eliminates the need for temporary shutdowns or manual interventions, which is crucial for maintaining consistent performance in applications requiring constant motion.
- Performance Stability: By maintaining and isolating fluid connections, an air rotary union ensures that the transferred media retain their critical pressure, temperature, and flow levels. This is essential for optimal machine performance and directly translates into higher output quality and fewer errors.
Air rotary unions enable significant efficiency gains across various sectors:
- Manufacturing: In general manufacturing, air rotary unions facilitate the seamless operation of pneumatic tools, robotic arms, and other equipment, boosting overall efficiency and reducing downtime.
- Automation: For automated assembly lines, rotary indexing machines (which rely on components like air rotary unions) allow multiple tasks to be performed in parallel. This drastically shortens cycle times and increases daily output. This “task overlapping” approach reduces delays inherent in linear systems, leading to substantial productivity boosts.
- Robotics: In robotic arms, air rotary unions are crucial for transmitting air or fluid to end-effectors, enabling the precise and continuous movements required for complex tasks.
The core mechanism by which an air rotary union boosts efficiency and productivity is the multiplier effect of its continuous flow. The consistent emphasis on “continuous operation,” “uninterrupted flow,” “seamless transfer,” and “reduced downtime” highlights how these components eliminate interruptions in fluid transfer, enabling continuous, parallel processing in automated systems. An air rotary union doesn’t just enable movement; it optimizes the speed and consistency of your industrial processes, driving faster cycle times and higher throughput.
3: Extended Machine Lifespan and Reduced Wear
Air rotary unions play a vital role in extending the operational life of your machinery and minimizing wear. This is primarily achieved through their superior sealing designs and effective friction management.
- Reduced Friction and Wear: By facilitating smooth rotation, an air rotary union significantly lowers friction between moving parts. This reduction not only extends machine lifespan but also enhances overall efficiency and cost-effectiveness. Advanced sealing materials like carbon graphite, silicon carbide, and PTFE, with their low friction coefficients and excellent wear resistance, help minimize wear and prevent heat buildup.
- Contamination Prevention: An air rotary union uses effective sealing mechanisms to prevent leaks and the entry of contaminants into your system. This ensures the cleanliness of the transferred fluid and optimizes machine performance, even in harsh conditions. Features like labyrinth seals can effectively shield bearings from contamination, maximizing their lifespan.
- Balanced Seal Design: The design of balanced mechanical seals minimizes pressure on the seal faces, further reducing friction and wear. This design helps extend the life of the seals and ensures the air rotary union remains reliable during prolonged operation.
- Adaptability to Extreme Conditions: High-quality air rotary unions are built to withstand a wide range of demanding operating conditions, including high pressures, high speeds, and broad temperature ranges. This inherent durability ensures reliable performance in challenging environments, reducing downtime caused by component failure.
By ensuring the seamless transfer of compressed air, an air rotary union prevents mechanical stress that could arise from fluid supply interruptions, indirectly extending machine life. Furthermore, superior sealing and bearing designs directly contribute to reducing friction and wear, prolonging the life of the air rotary union itself, and consequently protecting the machinery it serves.
4: Unparalleled Versatility and Adaptability
Air rotary unions are truly versatile components in industrial applications. Their ability to handle various media, adapt to different operational parameters, and offer diverse configurations makes them an ideal choice for countless industries and scenarios.
Media Compatibility: An air rotary union isn’t just for compressed air. They’re engineered to be compatible with a wide array of other fluids, including coolants, hydraulic oils, water, steam, vacuum, and even combinations of multiple media. Multi-passage air rotary unions, for instance, can simultaneously transfer different media through independent channels, effectively preventing cross-contamination.
Operating Parameter Adaptability: An air rotary union can withstand a broad spectrum of operating conditions, including extreme temperatures, pressures, and flow rates. They can be designed for pressures up to 15,000 PSI and speeds up to 40,000 RPM, ensuring reliable performance even in the most demanding applications.
Diverse Configurations and Designs: You’ll find air rotary unions in various sizes, shapes, and configurations, including single-passage, multi-passage, straight-through, 90-degree angle, and designs with bushings or bearings. They can also be custom-designed to meet your unique space and performance requirements. Miniature air rotary unions, for example, are perfect for space-constrained applications.
Integration with Electrical Slip Rings and Fiber Optic Rotary Joints: For comprehensive solutions, air rotary unions can be integrated with electrical slip rings and fiber optic rotary joints. This allows for the simultaneous transmission of fluids, electrical power, and data signals within a single component. This hybrid design is especially valuable in complex systems where space is limited and multiple transmission capabilities are needed.
Air rotary unions show remarkable adaptability across a wide range of industrial applications, making them truly indispensable. They are extensively used in:
- Machine Tools: For cooling and lubricating spindles, chuck clamping, tool sensing, and rotary index tables.
- Automotive Manufacturing: Crucial in assembly line operations, pneumatic tools, clutches, and brakes, meeting the high-speed and precision demands of modern automotive production.
- Packaging and Printing: Used for heating and cooling rolls, pneumatic clutches and brakes, and temperature control of ink and chill rolls in printing presses.
- Automation and Robotics: Essential in robotic arms for transferring air or fluid to end-effectors, enabling precise gripping and transfer movements.
- Agriculture and Construction: Employed in tire pressure control systems, hydraulic systems, and various heavy equipment for clutches and variable-speed drives.
- Other Industries: Including steel (cooling of rolls), oil and gas (pneumatic clutches and brakes on drilling rigs), semiconductor (miniature rotary unions), energy production (wind turbines), and food and pharmaceutical (requiring stainless steel construction).
This broad application range demonstrates how air rotary unions can adapt to various media types, pressures, speeds, and temperature specifications. They offer both standard products and custom-designed solutions to meet unique application needs.
This table shows typical operating parameters for different types of air swivels:
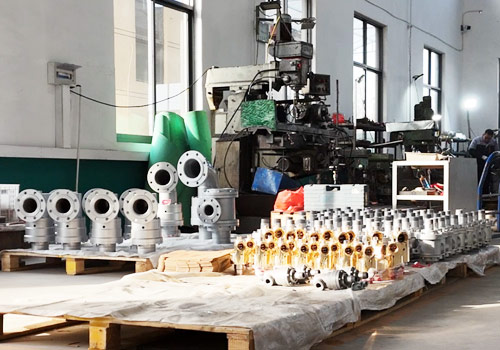
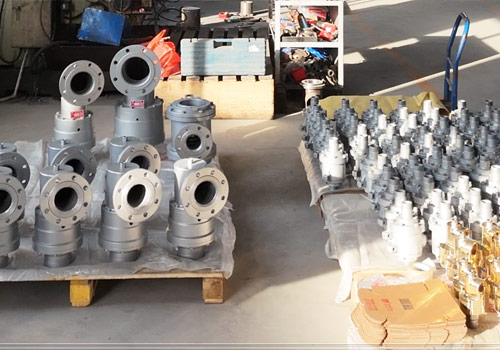
Characteristic / Type | Single Passage Air Rotary Union (General Purpose) | Multi-Passage Air Rotary Union (General Purpose) | High-Speed Air Rotary Union | Low-Speed Air Rotary Union |
---|---|---|---|---|
Passage Configuration | Single passage | 2 to 12 independent passages (more customizable) | Single or multi-passage | Single or multi-passage |
Typical Max Air Pressure | 50 bar (approx. 725 PSI); miniature unions up to 75 PSI | 250 PSI; some up to 4,500 psig (310 bar) | 250 PSI | 220 PSI; some up to 7,000 PSI |
Typical Max Rotational Speed | 3,500 RPM; general purpose 0-1,000 RPM; miniature unions up to 7,000 RPM | 250 RPM; some up to 250 RPM | 4,000 RPM; some up to 40,000 RPM | 0-380 RPM; some up to 250 RPM |
Typical Max Temperature | 121°C (250°F); general purpose up to 400°F (204°C) | 93°C (200°F); some up to 225°F (107°C) | 225°F (107°C) | 150°F (65°C); some up to 200°C |
Common Seal Types | Mechanical seals, O-ring seals, PTFE seals | PTFE seals, mechanical seals | Mechanical face seals (carbon graphite-carbide, silicon carbide-carbon graphite) | O-ring seals; special O-ring seals |
Key Features | Compact design, low friction, durable | Independent channels prevent cross-contamination, can integrate slip rings, absorb side loads | Low torque, full flow design, precision ball bearings, can integrate slip rings | Low torque, lightweight aluminum housing, thru-bore design, economical |
5: Significant Cost Savings and Reduced Downtime
Air rotary unions are crucial for reducing downtime and maintenance costs in your industrial operations. This economic benefit comes from their exceptional reliability, durability, and simplified maintenance.
Reduced Unexpected Downtime: An air rotary union significantly boosts equipment reliability through its efficient sealing and leak reduction capabilities. Older sealing methods often led to frequent downtime, wasted resources, and continuous maintenance issues due to leaks and wear. Modern air rotary unions, however, offer superior sealing performance, especially under high temperature and pressure, thereby minimizing unexpected downtime and boosting system efficiency.
Extended Component Lifespan: Built with advanced materials and precision engineering, an air rotary union can operate reliably for many years, even in harsh conditions. For example, silicon carbide seal rings excel under high load, high speed, and extreme conditions, offering outstanding resistance to abrasion, wear, chemicals, and thermal shock. This extended lifespan means less frequent component replacements, directly lowering your material costs and the labor expenses for replacement.
Simplified Maintenance: Many modern air rotary union designs are built for easy maintenance, featuring “quick replacement designs” and “on-machine seal replacement” capabilities. Some models even have lubricated-for-life bearings, further reducing your maintenance needs. Regular audits, predictive maintenance, correct alignment, and using original manufacturer spare parts are key to preventing air rotary union failures, extending their lifespan, and reducing unexpected maintenance costs.
Optimized Energy Consumption: The efficient sealing and reduced leakage of an air rotary union prevent the loss of compressed air or other fluids, leading to lower utility bills. In applications requiring precise fluid transfer control, this efficiency directly translates into lower energy consumption, saving you operational costs.
Avoiding Risks of Inferior Products: While choosing low-priced or “knock-off” air rotary unions might seem like a saving in the short term, it often means low product quality and inadequate support. This can lead to frequent failures, increased downtime, warranty issues, and damage to your company’s reputation. Investing in high-quality, proven air rotary unions, though potentially a higher initial cost, yields significant long-term savings by enhancing equipment availability, reducing maintenance demands, and preventing production interruptions.
The contribution of air rotary unions to reduced downtime and maintenance costs goes beyond simple savings. Their efficient sealing prevents fluid loss, leading to lower utility bills and improved equipment reliability. This directly reduces downtime and maintenance costs by lessening the need for frequent repairs and ensuring more reliable equipment operation.
Kesimpulan
Pneumatic sendi putar are critical components that ensure smooth, continuous and efficient industrial operations. These “behind-the-scenes heroes” provide seamless, leak-free fluid transfer through advanced engineering, ensuring product quality while protecting operators and the environment.
By ensuring a steady flow of compressed air, pneumatic rotary joints minimize friction and prevent contamination, resulting in significant productivity gains and extended machinery life. Pneumatic rotary joints are versatile and can be used in a wide range of industrial applications from machine tools to robotics.
By reducing downtime and maintenance costs, these advantages ultimately lead to significant economic benefits. At Modern Seals, we provide high-quality pneumatic rotary joint solutions to increase equipment availability, optimize energy consumption, and enhance your company’s profitability and competitive advantage.
Tanya Jawab Umum
What is an serikat putar udara and how does it work?
An air rotary union, also known as a pneumatic rotary joint or rotating union, is a mechanical device that facilitates the transfer of compressed air or other gases from a stationary supply line to a rotating piece of machinery. It works by creating a sealed connection between the fixed and rotating parts. As the rotating component turns, the air rotary union’s internal mechanism allows compressed air to flow into the device, holding it within during rotation. The air is then released when internal valve openings align with the outlet, ensuring a continuous and uninterrupted flow without the supply hose twisting or being damaged. This precision engineering ensures 360-degree rotation without leaks or loss of pressure.
What are the different types of seals used in air rotary unions?
Air rotary unions utilize various sealing mechanisms to prevent leaks and minimize friction. Common types include O-rings, lip seals, and more complex mechanical face seals. Mechanical seals often feature materials like carbon graphite, silicon carbide, or PTFE, which are chosen for their low friction coefficients and excellent wear resistance. Some advanced designs incorporate spring-loaded mechanical seals or hydrostatic seals for enhanced performance and extended life.
Can air rotary unions handle multiple types of media simultaneously?
Yes, air rotary unions can be designed to handle multiple types of media simultaneously. Multi-passage air rotary unions feature independent flow paths that allow different media, such as compressed air, coolants, hydraulic oils, or even vacuum, to be transferred concurrently without mixing or cross-contamination. This versatility is particularly valuable in complex systems where various fluids are needed for different functions within a rotating machine.
What factors should be considered when choosing an air rotary union?
When selecting an air rotary union, consider the type of media to be transferred, the operating pressure, temperature, and rotational speed. Other important factors include the number of passages required, connection sizes, flow requirements, and the physical dimensions or space constraints of your application. Material compatibility with the fluid and environmental conditions is also crucial for optimal performance and longevity.
How do air rotary unions contribute to efficiency and productivity?
Air rotary unions enhance operational efficiency and productivity by ensuring a seamless and continuous flow of compressed air or gases to rotating machinery. This uninterrupted supply allows pneumatic tools, robotic arms, and other equipment to operate continuously and efficiently, eliminating the need for temporary halts or manual interventions. Their reliability minimizes downtime, as they can function for extended periods without frequent maintenance or repairs, directly leading to improved productivity and consistent output in manufacturing processes.