
Selamat Datang di blog saya!
Sebelum kita menyelami kontennya, saya ingin Anda bergabung dengan saya di platform media sosial tempat saya berbagi lebih banyak wawasan, berinteraksi dengan komunitas, dan mengunggah berita terkini. Berikut cara Anda dapat terhubung dengan saya:
Facebook:https://www.facebook.com/profile.php?id=61575858997962
Sekarang, mari kita mulai perjalanan kita bersama. Saya harap Anda menemukan konten di sini yang berwawasan, menarik, dan berharga.
Daftar isi
Perkenalan
In complex industrial piping systems, the right components often determine operational efficiency. Metal expansion joints are critical to controlling thermal expansion, vibration and misalignment of piping to ensure longevity and safety.At Modern Sealing, a trusted leader in rotary joints and fluid sealing solutions, we understand the importance of precision-engineered components. With decades of dynamic and static sealing expertise, we are committed to helping industries achieve seamless operations.
This comprehensive guide answers one key question: how do you choose the right metal expansion joint for your system? Whether you’re an engineer, purchasing specialist, or facility manager, this blog provides practical insights to help you make informed decisions that ensure optimal performance and cost-effectiveness.
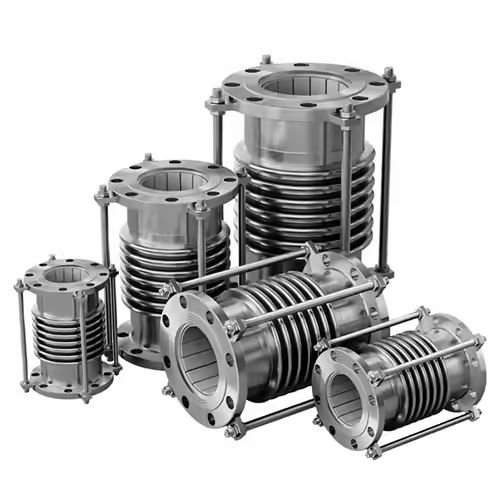
Understanding Metal Expansion Joints
What Are Metal Expansion Joints?
Metal expansion joints are flexible connectors designed to absorb movements in piping systems caused by thermal expansion, contraction, vibration, or pressure. Typically made from stainless steel, Inconel, or other durable alloys, these joints accommodate axial, lateral, and angular movements while maintaining a secure seal. They are indispensable in industries like power generation, chemical processing, oil and gas, and HVAC systems, where pipelines endure extreme conditions.
Why Are They Important?
Piping systems face constant stress from temperature fluctuations, mechanical vibrations, and structural shifts. Without metal expansion joints, these stresses can lead to pipe cracks, leaks, or catastrophic failures. By incorporating these joints, you protect equipment, reduce maintenance costs, and enhance system reliability. Their ability to handle high temperatures and corrosive environments makes them a preferred choice for demanding applications.
Key Factors in Choosing Metal Expansion Joints
Selecting the appropriate metal expansion joints requires careful consideration of several factors. Below, we explore the critical elements to guide your decision-making process.
Application Requirements
The first step is understanding your system’s specific needs. Consider the type of movement—axial (along the pipe’s axis), lateral (side-to-side), or angular (rotational). For instance, a power plant may require joints that handle high axial movement due to intense thermal expansion, while a chemical processing facility might prioritize corrosion resistance. Assessing the operating conditions, such as temperature, pressure, and media type, is crucial to ensure compatibility.
Material Selection
The choice of material for metal expansion joints significantly impacts performance. Common materials include:
- Stainless Steel: Ideal for general-purpose applications due to its corrosion resistance and durability.
- Inconel: Suited for high-temperature environments, such as exhaust systems.
- Hastelloy: Excellent for highly corrosive media, common in chemical plants.
- Monel: Offers superior resistance to saltwater corrosion, ideal for marine applications.
Selecting a material that matches your system’s environmental conditions ensures longevity and minimizes maintenance.
Design Specifications
Metal expansion joints come in various designs, such as single bellows, double bellows, or universal joints. The design must align with the expected movement and system constraints. For example, universal joints are suitable for systems requiring lateral and angular flexibility, while single bellows joints are better for straightforward axial movements. Additionally, consider factors like bellows thickness, convolution count, and end fittings to ensure compatibility with your piping system.
Compliance with Standards
Ensure the metal expansion joints meet industry standards, such as those set by the Expansion Joint Manufacturers Association (EJMA) or ASME. Compliance guarantees quality, safety, and performance under specified conditions. At Modern Sealing, our expertise in dynamic sealing ensures our solutions align with rigorous industry benchmarks, providing peace of mind for our clients.
Comparing Common Types of Metal Expansion Joints
To help you better understand the options available, the following table outlines key characteristics of common metal expansion joint types. This comparison focuses on functionality and application suitability rather than brand-specific details.
Type | Movement Type | Best Applications | Advantages | Considerations |
---|---|---|---|---|
Single Bellows | Axial | Power plants, HVAC systems | Simple design, cost-effective | Limited to axial movement |
Universal Bellows | Axial, Lateral, Angular | Complex piping systems, chemical plants | High flexibility, multi-directional movement | Higher cost, larger footprint |
Tied Universal | Lateral, Angular | Systems with restricted axial movement | Prevents axial extension, compact | Requires precise anchoring |
Hinged | Angular | Pipelines with rotational movement | Controlled angular movement | Not suitable for axial or lateral movement |
Gimbal | Multi-directional Angular | Aerospace, marine applications | Handles complex angular movements | Complex design, higher maintenance |
This table serves as a quick reference to match joint types with your system’s requirements. Always consult with engineers to verify compatibility with your specific setup.
Installation and Maintenance Best Practices
Proper Installation
Correct installation of metal expansion joints is critical to their performance. Misalignment or improper anchoring can lead to premature failure. Follow these best practices:
- Alignment: Ensure the joint is installed without undue stress or torsion.
- Anchoring: Use appropriate anchors and guides to control movement and prevent buckling.
- Inspection: Verify that end fittings and bellows are free from defects before installation.
Working with experienced manufacturers like Modern Sealing ensures access to expert guidance during installation, minimizing risks and maximizing joint lifespan.
Routine Maintenance
Regular maintenance extends the life of metal expansion joints. Schedule periodic inspections to check for signs of wear, corrosion, or fatigue. Monitor operating conditions to ensure they remain within the joint’s design parameters. Cleaning the bellows and checking for debris buildup can also prevent operational issues. A proactive maintenance plan reduces downtime and costly repairs.
Environmental and Operational Considerations
Temperature and Pressure Extremes
Metal expansion joints must withstand the operating environment’s temperature and pressure. For high-temperature applications, such as steam pipelines, select joints with robust materials like Inconel. For high-pressure systems, ensure the joint’s pressure rating exceeds the maximum operating pressure to avoid failures.
Corrosive Media
In industries like chemical processing, pipelines often transport corrosive fluids. Choosing metal expansion joints with materials resistant to specific chemicals is essential. For example, Hastelloy is ideal for acidic environments, while stainless steel suits less aggressive media. Always consult material compatibility charts to make informed choices.
Vibration and Noise Reduction
Metal expansion joints also mitigate vibration and noise in piping systems. In applications like HVAC or industrial exhaust systems, joints with multiple convolutions can absorb vibrations effectively, reducing wear on adjacent components and improving workplace safety.
Cost vs. Performance Trade-Offs
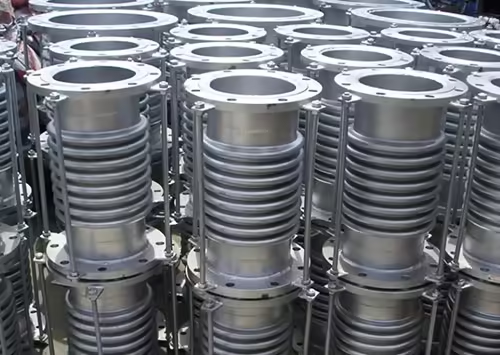
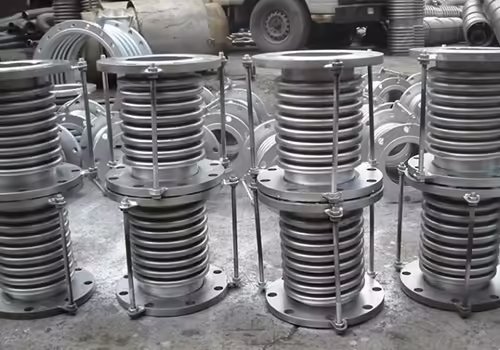
While cost is a significant factor, prioritizing quality over price ensures long-term savings. Cheaper metal expansion joints may fail prematurely, leading to costly repairs or replacements. Investing in high-quality joints from reputable manufacturers, balances upfront costs with durability and performance. At Modern Sealing, our patented technologies and rigorous quality control deliver reliable solutions that optimize your budget.
Kesimpulan
Choosing the right metal expansion joint is critical; it affects the safety, efficiency and longevity of your piping system. Modern Seal’s decades of expertise in rotary joints, metal hoses, and fluid sealing solutions allow us to customize high-quality, proprietary components to meet your needs.
Ready to find the perfect solution for your needs? Contact Modern Sealing to learn more about our high-quality, patented metal expansion joints that will improve your system’s performance.
Tanya Jawab Umum
What factors should I consider when selecting a metal expansion joint?
Key factors include operating pressure and temperature, movement type (axial, lateral, angular), media compatibility, installation space, and cycle life requirements.
Are metal expansion joints suitable for both thermal and mechanical movement?
Yes. Metal expansion joints are designed to absorb both thermal expansion and mechanical vibration or movement in piping systems, making them highly versatile.
How do I choose between single and multi-ply bellows?
Single-ply bellows are best for standard applications with moderate pressure. Multi-ply bellows offer higher flexibility and fatigue resistance for demanding or high-cycle environments.
What materials are commonly used for metal expansion joints?
Stainless steel (304, 316L, 321), Inconel, and Hastelloy are common due to their high strength, corrosion resistance, and temperature tolerance.
How often should metal expansion joints be inspected or replaced?
Inspection frequency depends on the application, but annual inspections are common. Replacement is typically needed when cracks, deformation, or leakage is observed, or after the rated cycle life.
What’s the difference between axial and lateral movement in expansion joints?
Axial movement refers to compression/extension along the pipe axis. Lateral movement is perpendicular to the pipe axis. Some joints are designed to handle both types.